What is Porosity in Welding: Recognizing Its Reasons and Enhancing Your Abilities
Wiki Article
Porosity in Welding: Identifying Common Issues and Implementing Finest Practices for Avoidance
Porosity in welding is a prevalent issue that commonly goes unnoticed up until it causes considerable troubles with the integrity of welds. In this conversation, we will certainly explore the vital aspects contributing to porosity formation, examine its damaging effects on weld performance, and review the best methods that can be taken on to lessen porosity occurrence in welding procedures.Common Sources Of Porosity
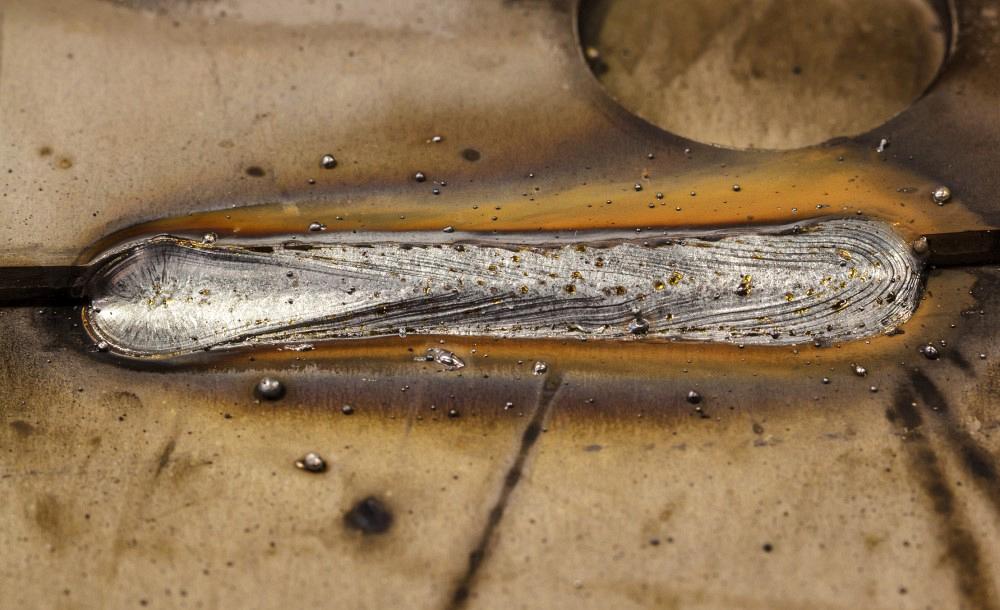
Using dirty or damp filler products can introduce pollutants into the weld, contributing to porosity concerns. To reduce these common reasons of porosity, complete cleansing of base steels, appropriate protecting gas choice, and adherence to optimal welding parameters are important techniques in achieving high-quality, porosity-free welds.
Effect of Porosity on Weld Quality

The visibility of porosity in welding can considerably compromise the architectural integrity and mechanical residential or commercial properties of welded joints. Porosity develops gaps within the weld metal, compromising its general stamina and load-bearing capacity.
Welds with high porosity degrees tend to exhibit lower effect toughness and lowered capability to warp plastically before fracturing. Porosity can impede the weld's ability to efficiently transfer pressures, leading to early weld failing and possible safety and security dangers in vital structures.
Ideal Practices for Porosity Avoidance
To boost the architectural integrity and top quality of bonded joints, what specific steps can be applied to lessen the occurrence of porosity throughout the welding process? Utilizing the correct welding strategy for the particular product being welded, such as adjusting the welding angle and gun setting, can additionally protect against porosity. Regular assessment of welds and prompt remediation of any kind of issues determined during the welding process are crucial practices to prevent porosity and produce top quality welds.Significance of Appropriate Welding Methods
Executing correct welding techniques is critical in making certain the structural stability and top quality of bonded joints, building on the structure of efficient porosity prevention measures. Welding techniques straight influence the overall strength and toughness of the bonded structure. One essential element of appropriate welding strategies is click here for more info keeping the Continued appropriate heat input. Too much warmth can cause enhanced porosity due to the entrapment of gases in the weld pool. On the other hand, inadequate warm might cause incomplete fusion, developing prospective weak points in the joint. In addition, utilizing the appropriate welding criteria, such as voltage, present, and travel rate, is important for achieving audio welds with very little porosity.Additionally, the choice of welding procedure, whether it be MIG, TIG, or stick welding, must line up with the particular requirements of the task to make sure ideal outcomes. Proper cleaning and prep work of the base steel, as well as choosing the right filler material, are additionally crucial elements of competent welding techniques. By sticking to these best practices, welders can reduce the danger of porosity development and produce premium, structurally audio welds.
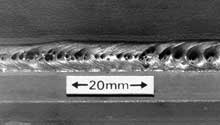
Examining and Quality Assurance Steps
Testing treatments are essential to spot and avoid porosity in welding, guaranteeing the stamina and sturdiness of the final product. Non-destructive screening approaches such as ultrasonic testing, radiographic testing, and aesthetic inspection are frequently used to identify prospective flaws like porosity.Post-weld inspections, on the various other hand, analyze the last weld for any type of defects, consisting of porosity, and validate that it satisfies specified criteria. Applying a detailed top quality control plan that includes complete testing procedures and assessments is critical to reducing porosity concerns and making sure the overall top quality of welded joints.
Conclusion
To conclude, porosity in welding can be a typical issue that influences the top quality of welds. By identifying the common sources of porosity and executing finest techniques for prevention, such as proper welding methods and testing procedures, welders can guarantee high top quality and reputable welds. It is important to focus on prevention techniques to lessen the incident of porosity check out here and preserve the stability of welded structures.Report this wiki page